Understanding Plastic Injection Molding Tolerances: A Comprehensive Guide
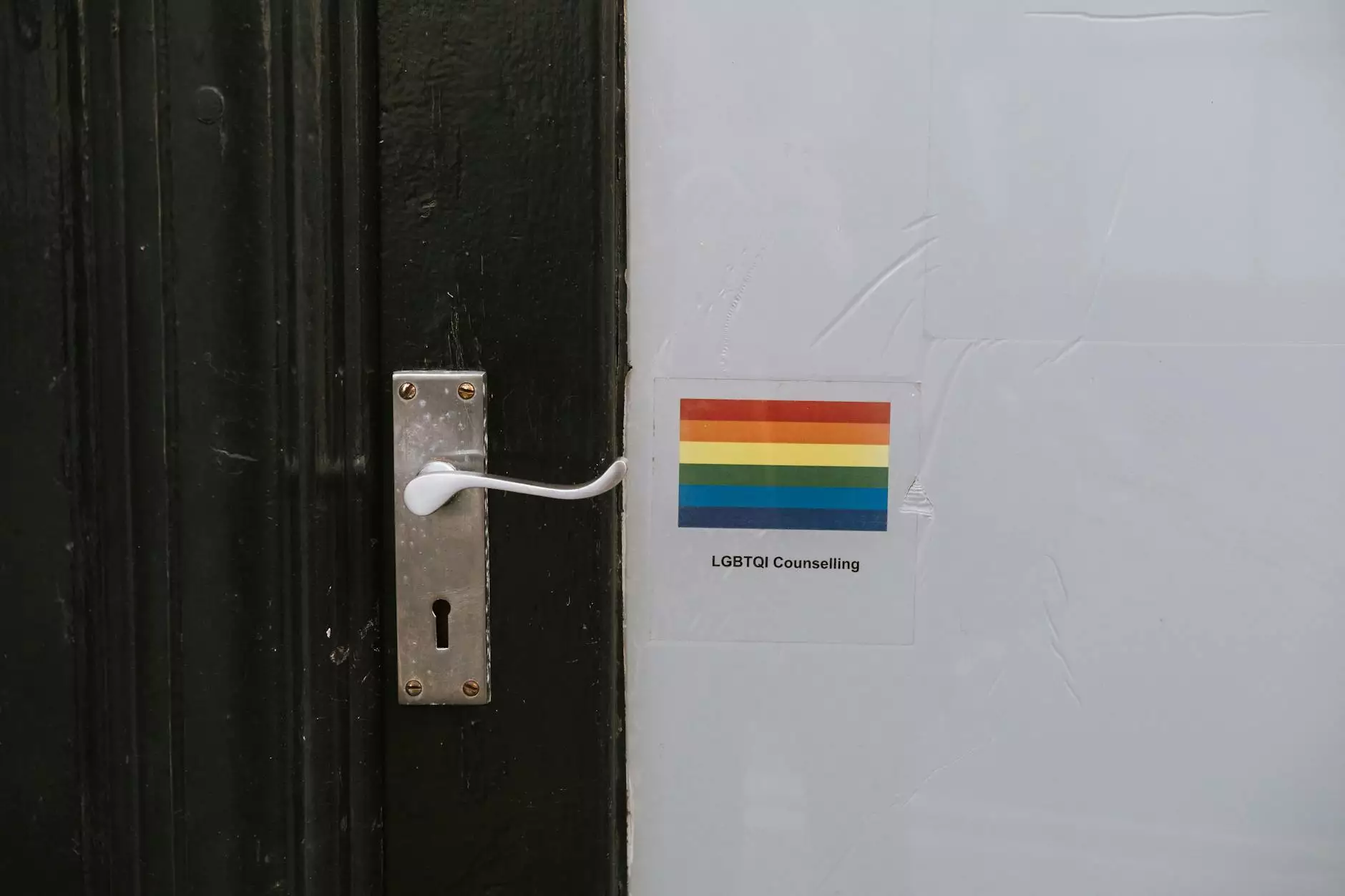
In the world of manufacturing and production, plastic injection molding is one of the most significant processes used to create various components and products. However, the effectiveness of this process hinges on a critical aspect known as tolerances. This guide delves deep into plastic injection molding tolerances, exploring their definition, significance, and the best practices for achieving precise results.
What Are Plastic Injection Molding Tolerances?
Molding tolerances refer to the allowable variations in dimensions when manufacturing parts. In plastic injection molding, this is crucial because even the slightest deviation can lead to production failures. The tolerances define the acceptable limits of variation in the dimensions and form of the molded parts, ensuring that each part fits within specified requirements.
The Importance of Tolerances in Injection Molding
Plastic injection molding tolerances play a pivotal role in several aspects:
- Quality Control: Ensuring that each part adheres to specified tolerances is vital for maintaining high-quality standards.
- Interchangeability: Precise tolerances enable parts to be interchangeable with ease, a necessity in mass production.
- Functionality: Proper tolerances guarantee that the parts function as intended within their applications.
- Cost Efficiency: Maintaining tolerances can reduce waste and rework, leading to cost savings for manufacturers.
Factors Influencing Plastic Injection Molding Tolerances
Achieving the right tolerances in injection molding involves several factors:
1. Material Selection
The type of plastic material used significantly affects tolerances. Different materials have varying shrinkage rates and deformation characteristics which must be accounted for in the mold design.
2. Mold Design
A well-designed mold is essential for producing parts within tolerance. Factors such as cooling channels, venting, and mold materials all contribute to the overall accuracy of the molded parts.
3. Processing Conditions
The parameters set during the injection molding process, including temperature, pressure, and injection speed, can influence the final dimensions of the parts. Operators must maintain consistency in these settings to achieve the desired tolerances.
4. Cooling Rate
The rate at which the plastic cools and solidifies affects shrinkage. Uneven cooling can lead to warping or distortion of the parts, making it essential to control cooling to maintain tolerances.
Common Plastic Injection Molding Tolerance Standards
Several standards can guide manufacturers in setting tolerances for plastic injection molded components. Two of the most recognized are:
1. ISO 2768
This standard provides general tolerances for linear dimensions without individual tolerance indications. It serves as a guideline for manufacturing processes.
2. ASME Y14.5
The American Society of Mechanical Engineers (ASME) standard outlines geometric dimensioning and tolerancing (GD&T) practices, which help in the precise definition of tolerances for complex geometries.
Best Practices for Achieving Tolerances in Injection Molding
To ensure plastic injection molding tolerances are met, consider implementing the following best practices:
1. Collaborate during the Design Phase
Working closely with design engineers can help analyze and establish snug tolerances that can realistically be achieved through injection molding.
2. Utilize Simulation Software
Employing advanced simulation software can predict how changes in design, materials, and processes will affect the final product, allowing for adjustments before actual production.
3. Conduct Regular Equipment Maintenance
Maintaining and calibrating injection molding machines regularly ensures consistent operation and minimizes the risks of dimensional deviations.
4. Develop a Robust Quality Control System
A diligent quality control process helps in identifying parts that fall outside of the acceptable tolerances, facilitating immediate remediation to prevent defective parts from reaching consumers.
Challenges in Maintaining Plastic Injection Molding Tolerances
While achieving the right tolerances is crucial, several challenges often arise during production:
1. Environmental Factors
Changes in temperature and humidity can affect material properties and cooling times, leading to potential deviations in measurements.
2. Material Variability
Different batches of the same material can possess slight variations in properties that may affect shrinkage and final dimensions.
3. Machine Wear and Tear
Over time, the precision of molds and machinery can diminish, impacting their ability to produce parts within tolerance. Regular monitoring and maintenance are required to mitigate this risk.
Case Studies and Real-World Applications
Understanding the practical application of plastic injection molding tolerances is crucial. Here are some examples:
1. Automotive Industry
In automotive manufacturing, components such as dashboard parts and electrical housings must meet strict tolerances to ensure safety and functionality. By adhering to established industry tolerances, manufacturers ensure seamless integration into larger assemblies.
2. Medical Devices
Medical device production requires the highest level of precision. Injection molding tolerances are critical for parts such as syringes or surgical instruments where even minute deviations can have significant consequences.
3. Consumer Electronics
In the production of consumer electronics, such as smartphones and tablets, openings for buttons, speakers, and camera lenses must fit precisely. Adhering to tight tolerances allows for aesthetic and functional excellence.
Future Trends in Plastic Injection Molding Tolerances
The manufacturing industry is continually evolving, and so are the methods for maintaining tolerances in plastic injection molding. Upcoming trends include:
1. Smart Manufacturing
With advancements in IoT (Internet of Things), manufacturers can monitor processes in real-time, allowing for rapid adjustments that help maintain tolerances effectively.
2. Advanced Materials
As new materials are developed with better properties, the potential for improved precision in injection molding increases, allowing for tighter tolerances.
3. Automation and Robotics
The rise of automation within the manufacturing process enhances consistency in production, directly impacting the ability to maintain stringent tolerances.
Conclusion: The Critical Role of Tolerances in Plastic Injection Molding
In conclusion, plastic injection molding tolerances are a fundamental component of the manufacturing process. They ensure that parts are produced accurately, meet quality standards, and function as intended. By understanding and implementing best practices, manufacturers can navigate challenges and leverage advancements in technology to optimize their production processes.
As the industry continues to evolve alongside technological improvements, a focus on tolerances will remain imperative for those in the field, particularly in sectors such as metal fabrication where precision is non-negotiable. To explore more about this and other relevant topics, visit deepmould.net.